Hudson Jeans Definition
Source(Google.com.pk)The completed pair of blue jeans is I0 then pressed. They are placed into a large pressing machine that steam irons the entire garment at once in about a minute. A size tag is punched into the material and the jeans are folded, stacked, and placed in boxes according to style, color, and size before being sent to the warehouse for storage. When the jeans are selected to be sent to a store, they are put in large shipping cartons and sent on freight trains or trucks.
After being crafted into an article of clothing, most denim is washed to make it softer and to reduce or eliminate shrinkage which could cause an item to not fit after the owner washes it. In addition to being washed, non-dry denim is sometimes artificially "distressed" to produce a worn look.
Much of the appeal of factory distressed denim is that it looks similar to dry denim that has, with time, faded. With dry denim, however, such fading is affected by the body of the person who wears the jeans and the activities of his/her daily life. This creates what many enthusiasts feel to be a more natural, unique look than distressed denim.
To facilitate the natural distressing process, some wearers of dry denim will often abstain from washing their jeans for more than six months, though it is not a necessity for fading.
All Fabric has a selvedge (a words
derived from the joining of "self" & "edge"), this is
the natural edge of the cloth and contrary to some sources does not unravel or
fray.
"Selvage denim" refers to
a unique closed selvage (derived from the Latin Salvare, meaning "to
secure, to make safe") that is created using one continuous cross yarn
(the wefta) that is passed back and forth through the vertical warp beams. This is traditionally finished with a
contrast weft, most commonly red which is why sometimes this type of denim is
referred to as "Red Selvage". This process is only possible using a shuttle
loom
Shuttle looms weave a narrower 30
inch fabric, which is on average half the width of the more modern shuttleless
sulzer looms (invented in 1927 by the
Sulzer brothers) and thus a longer piece of fabric is required to make a pair
of jeans (approximately 3 yards). To maximize yield, jean where traditionally
made with a straight outseam that utalised the full width of the fabric
including this edge. This became not only desirable but since the production of
wider width denim, a mark of premium quality as when worn with a turn up the
two selvages where visable rather than a unatractive overlocked edge.
Originally Indigo was produced using
dye from plan indegofera tinctoria but
most denim today is dyed with synthetic. indigo In both cases the yarn will
undergo a repetitive sequence of dipping and oxidization, the more dipps, the
stronger the indigo shade.
Rope dye is considered the best yarn dying method as it eliminated shading
across the fabric width, thou the alternative slasher process is cheaper as
only one beaming process is needed (in rope dying, beaing is done twice). Fades
caused by prolonged periods of wear, without washing, have become the main
allure for raw denim. The fading patterns are a way of personalizing the
garment for each customer. These fades are categorized by certain namesWhiskers
– Faded streaks that surround the crotch area of the denim. Combs – Also known,
as “honey combs” are the streaks of faded lines that are found behind the knee.
Stacks – Produced by having the inseam of the denim hemmed a few inches longer
than actual leg length. The extra fabric stacks on top of the shoe causing a
fade to form around the ankle to calf area of the denim. Train Tracks – appears
on the outseams of the denim. This fade showcases the selvedge by forming two
sets of fades that resemble train tracks. Originally Indigo was produced using dye from
plant tinctoria but most denim today is dyed with synthetic. In both cases the
yarn will undergo a repetitive sequence of dipping and oxidization, the more
dipps, the stronger the indigo shade.Byproducts/Waste
The process of cloth making involves treating the fabric with a number of chemicals in order to produce clothing with such desirable characteristics such as durability, colorfastness, and comfort. Each step of finishing the cotton fabric (dyeing, sanforizing, etc.) produces byproducts, most of which are biodegradable.
Byproducts of denim manufacture include organic pollutants, such as starch and dye, which can be treated through biological methods. These organic wastes may not be dumped into streams or lakes because of their high biochemical oxygen demand. To decompose, such waste materials utilize so much oxygen that the lifeforms in the body of water would be denied the oxygen necessary for survival.
Denim manufacturers process their own wastes in compliance with all relevant government regulations.
Quality Control
Cotton is a desirable natural fiber for several reasons. Cloth made from cotton is wear resistant, strong, flexible, and impermeable. Blue jeans are only as good as the cotton that goes into them, however, and several tests exist for cotton fiber. All bales of cotton are inspected by the denim manufacturer for the desired color, fiber length, and strength. Strength is the most important factor in blue jeans. It is measured by using a weight to pull it. When the fiber breaks, the force used to break it is measured. The cotton's strength index (weight of weight divided by weight of sample) is then calculated.
The finished denim cloth is carefully inspected for defects. Each defect is rated on a government-defined scale ranging from one point for very small flaws to four points for major defects. Although government regulations allow cloth with a high defect rating to be sold, in reality customers will not accept denim with more than seven to ten defect points per square meter. Poor cloth is sold as damaged. Denim is also tested for durability and its tendency to shrink. Samples of cloth are washed and dried several times to see how they wear.
Hudson Jeans Free Images Photos Pictures Pics 2013

Hudson Jeans Free Images Photos Pictures Pics 2013

Hudson Jeans Free Images Photos Pictures Pics 2013

Hudson Jeans Free Images Photos Pictures Pics 2013

Hudson Jeans Free Images Photos Pictures Pics 2013
Hudson Jeans Free Images Photos Pictures Pics 2013

Hudson Jeans Free Images Photos Pictures Pics 2013

Hudson Jeans Free Images Photos Pictures Pics 2013
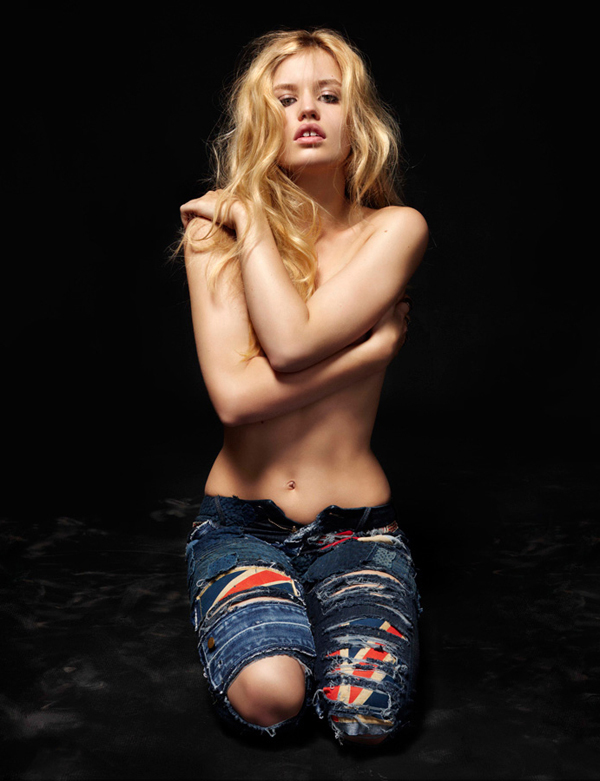
Hudson Jeans Free Images Photos Pictures Pics 2013

No comments:
Post a Comment