7 Jeans For Men Definition
Source(Google.com.pk)Once the desired design is selected, patterns from the design are cut from heavy paper or cardboard. Up to 80 different sizes are possible from one pattern. The pieces of denim are then cut with high speed cutting machines from stacks 100 layers thick. Excluding rivets, buttons, and zippers, a pair of blue jeans contains about ten different pieces, from the pockets to the leg panels to the waistband and belt loops.
The pieces of denim are ready to be sewn at this point. Sewing is done in an assembly line fashion, with rows of industrial human-operated sewing machines. Each sewer is assigned a specific function, such as making only back pockets. First, the various pockets and belt loops are assembled. Next, one sewer attaches the pockets to the leg seams, another then sews the leg seams together, and still another attaches the waist-band. Once the waist band is secure, the belt loops may be stitched on and the buttons attached. If the jeans include a zipper, it is then sewn into place, and the pants are hemmed. Finally, the rivets are placed in the appropriate places and the maker's label is sewn on last.
Some jeans are prewashed and/or stone-washed to alter the appearance or texture of the finished jeans. Prewashing involves washing the jeans in industrial detergent for a short time to soften the denim. Stone-washing also means washing the jeans, but pumice is added to the load, resulting in a faded appearance. Small stones (less than one inch [one centimeter] in diameter) produce an even abrasion, while large stones (about four inches [10 centimeters] in diameter) highlight the seams and pockets and produce a more uneven appearance.
The completed pair of blue jeans is I0 then pressed. They are placed into a large pressing machine that steam irons the entire garment at once in about a minute. A size tag is punched into the material and the jeans are folded, stacked, and placed in boxes according to style, color, and size before being sent to the warehouse for storage. When the jeans are selected to be sent to a store, they are put in large shipping cartons and sent on freight trains or trucks.
The process of cloth making involves treating the fabric with a number of chemicals in order to produce clothing with such desirable characteristics such as durability, colorfastness, and comfort. Each step of finishing the cotton fabric (dyeing, sanforizing, etc.) produces byproducts, most of which are biodegradable.
The word "selvage" comes from the phrase "self-edge", the natural edge of a roll of fabric. In this case, denim made on old-style shuttle looms. These looms weave fabric with one continuous cross thread (the weft) that is passed back and forth all the way down the length of the bolt. As the weft loops back into the edge of the denim it creates this “self-edge” or Selvage. Selvage is desirable because the edge can’t fray like lower grade denims that have separate wefts which leave an open edge that must be stitched. Shuttle looming is a more time-consuming weaving process that produces denim of a tighter weave resulting in a heavier weight fabric that lasts.
Shuttle looms weave a more narrow piece of fabric, and thus
a longer piece of fabric is required to make a pair of jeans (approximately 3
yards). To maximize yield, traditional jean makers use the fabric all the way
to the selvage edge. When the cuff is turned up the two selvage edges, where
the denim is sewn together, can be seen. The selvage edge is usually stiched
with colored thread: green, white, brown, yellow, and red (red is the most
common). Fabric mills used these colors to differentiate between fabrics. Most
selvage jeans today are dyed with synthetic indigo, but natural is available in smaller niche denim labels.
Loop dying machines feed a rope of cotton yarn through vats of indigo dye and
then back out. The dye is allowed to oxidize before the next dip. Multiple dips
create a deep dark indigo blue.
In response to increased demand for jeans in the 1950's,
American denim manufacturers replaced the old shuttle style looms with modern
projectile looms. The new looms produced fabric faster and wider (60-inches or
wider), yet lighter and less durable. Synthetic dyeing techniques along with
post-dye treatments were introduced to control shrink and twist.
7 Jeans For Men Free Images Photos Pictures Pics 2013
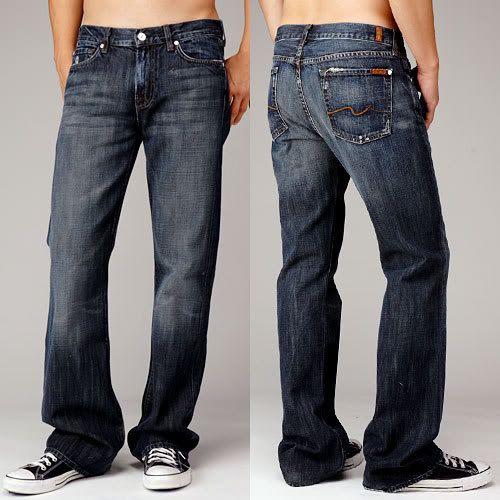
7 Jeans For Men Free Images Photos Pictures Pics 2013

7 Jeans For Men Free Images Photos Pictures Pics 2013

7 Jeans For Men Free Images Photos Pictures Pics 2013
7 Jeans For Men Free Images Photos Pictures Pics 2013
7 Jeans For Men Free Images Photos Pictures Pics 2013
7 Jeans For Men Free Images Photos Pictures Pics 2013

7 Jeans For Men Free Images Photos Pictures Pics 2013
7 Jeans For Men Free Images Photos Pictures Pics 2013

7 Jeans For Men Free Images Photos Pictures Pics 2013
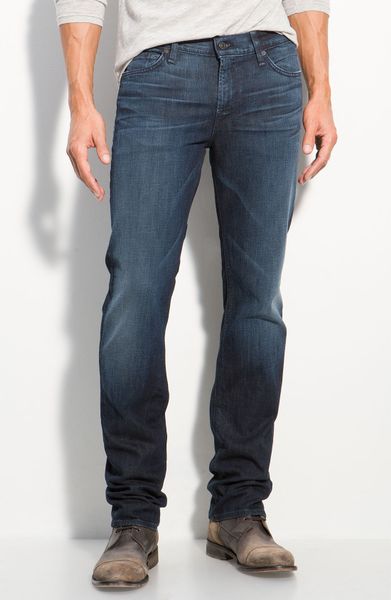
No comments:
Post a Comment