Designer Jeans Men Definition
Source(Google.com.pk)The dyed yarn is then slashed; that is, it is coated with sizing (any one of a variety of starchy substances) to make the threads stronger and stiffer. Once this operation is complete, the yarn threads are ready to woven with undyed filling yarn threads.
Weaving the yarn
The yarn is then woven on large mechanical looms. Denim is not 100 percent blue, as the blue dyed threads forming the warp(long, vertical threads) are combined with white threads forming the weft (shorter, horizontal threads). Because denim is woven with the blue threads packed closer together than the white threads and with the blue threads covering three out of four white threads, the blue threads dominate. (By examining a piece of denim closely one can detect the steep diagonal pattern that results from this process, which is known as a three-by-one right-hand twill weave.) Although mechanized looms make use of the same basic weaving procedure as a simple hand loom, they are much larger and faster. A modern "shuttle-less" loom (which uses a very small carrier instead of the traditional shuttle to weave the weft threads between the warp threads) may produce as much as 3,279 yards (3,000 meters) of cloth 3.28 or 4.37 yards (three or four meters) wide in a single week. As much as 1,093 yards (1,000 meters) of cloth may be rolled into a single huge bolt.
At this point the denim is ready for finishing, a term referring to a variety of treatments applied to cloth after it is woven. With denim, finishing is usually fairly simple. The cloth is brushed to remove loose threads and lint, and the denim is usually skewed in a way that will prevent it from twisting when it is made into clothing. The denim may then be sanforized, or preshrunk. Preshrunk denim should shrink no more than three percent after three washings.
Durable twill-woven fabric with coloured (usually
blue) warp (lengthwise) and white filling (crosswise) threads, also sometimes
woven in coloured stripes. The name originated in the French serge de Nîmes. Denim is usually all-cotten
though it is sometimes made of a cotton-synthetic mixture. Decades of use in
the clothing industry, especially in the manufacture of overalls and trousers
worn for heavy labour, have demonstrated denim's durability, a quality that,
along with its comfort, made denim jeans extremely popular for leisure wear in
the late 20th century.
a. A coarse twilled cloth,
usually cotton, used for jeans, overalls, and work uniforms.
b. denims Trousers or another
garment made of this cloth.
A
similar but finer fabric used in draperies and upholstery.
a heavy twill fabric of cotton or
other fibers woven with white and colored, often blue, threads, used esp. for
jeans.
a lighter, softer fabric resembling this..
denims, (used with a pl. v.) clothes of denim. Dry or raw denim,
as opposed to washed denim, is a denim fabric that is not washed after being
dyed during its production. Over time, denim will generally fade, which is
often considered desirable. During the process of wear, it is typical to see
fading on areas that generally receive the most stress, which includes the
upper thighs workers the ankles (stacks) and behind the knees honey comes
After being crafted into an article of clothing, most denim is washed to
make it softer and to reduce or eliminate shrinkage which could cause an item
to not fit after the owner washes it. In addition to being washed, non-dry
denim is sometimes artificially "distressed" to produce a worn look.Much of the appeal of factory distressed denim is that it looks similar to dry denim that has, with time, faded. With dry denim, however, such fading is affected by the body of the person who wears the jeans and the activities of his/her daily life. This creates what many enthusiasts feel to be a more natural, unique look than distressed denim.
Shuttle looms weave a narrower 30
inch fabric, which is on average half the width of the more modern shuttleless
sulzer looms (invented in 1927 by the
Sulzer brothers) and thus a longer piece of fabric is required to make a pair
of jeans (approximately 3 yards). To maximize yield, jean where traditionally
made with a straight outseam that utalised the full width of the fabric
including this edge. This became not only desirable but since the production of
wider width denim, a mark of premium quality as when worn with a turn up the
two selvages where visable rather than a unatractive overlocked edge.
Dying
Originally Indigo was produced using
dye from plan indegofera tinctoria but
most denim today is dyed with synthetic. indigo In both cases the yarn will
undergo a repetitive sequence of dipping and oxidization, the more dipps, the
stronger the indigo shade.
Rope dye is considered the best yarn dying method as it eliminated shading
across the fabric width, thou the alternative slasher process is cheaper as
only one beaming process is needed (in rope dying, beaing is done twice). Fades
caused by prolonged periods of wear, without washing, have become the main
allure for raw denim. The fading patterns are a way of personalizing the
garment for each customer. These fades are categorized by certain namesWhiskers
– Faded streaks that surround the crotch area of the denim. Combs – Also known,
as “honey combs” are the streaks of faded lines that are found behind the knee.
Stacks – Produced by having the inseam of the denim hemmed a few inches longer
than actual leg length. The extra fabric stacks on top of the shoe causing a
fade to form around the ankle to calf area of the denim. Train Tracks – appears
on the outseams of the denim. This fade showcases the selvedge by forming two
sets of fades that resemble train tracks. Originally Indigo was produced using dye from
plant tinctoria but most denim today is dyed with synthetic. In both cases the
yarn will undergo a repetitive sequence of dipping and oxidization, the more
dipps, the stronger the indigo shade.Rope dye is considered the best yarn dying method as it eliminated shading across the fabric width, thou the alternative slasher process is cheaper as only one beaming process is needed (in rope dying, beaing is done twice).
Making the blue jeans
Once the desired design is selected, patterns from the design are cut from heavy paper or cardboard. Up to 80 different sizes are possible from one pattern. The pieces of denim are then cut with high speed cutting machines from stacks 100 layers thick. Excluding rivets, buttons, and zippers, a pair of blue jeans contains about ten different pieces, from the pockets to the leg panels to the waistband and belt loops.
The pieces of denim are ready to be sewn at this point. Sewing is done in an assembly line fashion, with rows of industrial human-operated sewing machines. Each sewer is assigned a specific function, such as making only back pockets. First, the various pockets and belt loops are assembled. Next, one sewer attaches the pockets to the leg seams, another then sews the leg seams together, and still another attaches the waist-band.
Designer Jeans Men Free Images Photos Pictures Pics 2013

Designer Jeans Men Free Images Photos Pictures Pics 2013

Designer Jeans Men Free Images Photos Pictures Pics 2013

Designer Jeans Men Free Images Photos Pictures Pics 2013
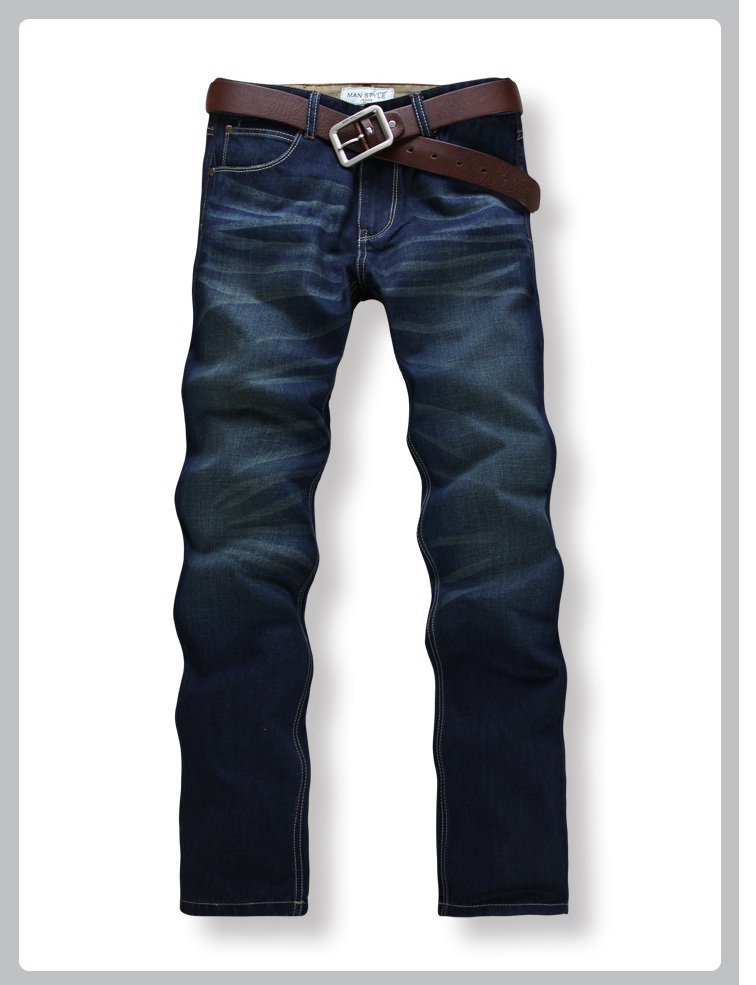
Designer Jeans Men Free Images Photos Pictures Pics 2013
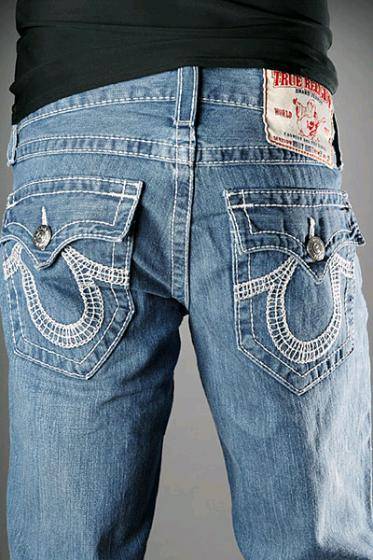
Designer Jeans Men Free Images Photos Pictures Pics 2013

Designer Jeans Men Free Images Photos Pictures Pics 2013
Designer Jeans Men Free Images Photos Pictures Pics 2013

Designer Jeans Men Free Images Photos Pictures Pics 2013

Designer Jeans Men Free Images Photos Pictures Pics 2013

No comments:
Post a Comment